Cladding allows the majority of the half to be made with cheap materials, whereas providing the floor with fascinating properties related to the more expensive cladding material. Laser cladding has resulted in surfaces with superb finish, good homogeneity, and really low porosity. Common materials used for cladding include carbides, iron-primarily based alloys, nickel base alloys, and cobalt base alloys. Laser cladding is a process in which a metal coating is applied onto the floor of an element utilizing a laser as the warmth source.
Depending on the supplies to be bonded, cleaning and roughening are finest carried out by brushing, grinding, or scraping utilizing a specifically designed cutter with needles. A suction removal unit is used to evacuate rigorously any material waste in order to avoid bonding flaws on account of poor adhesion. Laser cladding allows us to use metal layers for put on and corrosion protection with nice precision. In addition, it may be used to repair and modify parts.
Long-term, in-reactor, oxidation, and hydrogen decide up conduct of zircaloy-2 and Zr-2.5Â Nb strain tubes, showing parabolic after which accelerated linear oxidation and hydrogen pickup kinetics in zircaloy-2. A low and uniform price of corrosion and hydrogen decide up is seen in the in Zr-2.5Â Nb alloy. Differential swelling between cladding, wrapper tube, and spacing system (spacer wire or grids) can induce extra stresses and deformations on these components and/or generate coolant circulate perturbations within the bundle. These phenomena have been studied and have particularly shown that wires or grid supplies have to be chosen and specified so as to minimize differential swelling.
In our cladding solutions we consider the styling and hues, choice of materials, lighting design and general setting of the building as key CI parts, in order that every little thing matches your particular person necessities. Although the thermal properties of façade coverings was of primary importance, right now company identity (CI) elements are essential to the design of the panels. ACM (aluminium composite), glass, pure stone and sheet steel are simply some of the supplies that can be utilized in the big variety of plate-holders and sections. , the place T is absolutely the temperature and β is the burnup.
The oxidation process and the nature of the oxide layer on a zirconium alloy sample are schematically illustrated in Fig. 6 . Cladding is an outer layer of either vertical or horizontal materials, used to enhance the appearance, thermal insulation and the climate resistance of a constructing. Our cladding is out there in a variety of sizes, types of timber and surface finishes.
Moreover, embrittlement owing to irradiation or temperature needs to be mastered in order to avoid rupture within the reactor or through the again-end of the cycle (dealing with, washing, and so forth.). Cold-worked austenitic steels (with composition closed to that of the cladding) were used first however are actually frequently replaced by more swelling-resistant ferritic–martensitic steels (9Cr sort), in so far as the height wrapper temperature, lower than that of cladding, permits avoidance of thermal creep issues.
The filler materials can both be equipped in powder form e.g. as steel powder, or with a welding wire. When laser cladding is carried out using powder, the laser usually heats the workpiece with a defocussed laser beam and melts it locally. At the identical time, an inert fuel combined with a fine metallic powder is launched. The metal powder melts at the heated space and is fused to the floor of the workpiece.
The helium filling gasoline can also be a reasonably good conductor, however solely so long as it stays uncontaminated by fission products. The poorly conducting ceramic gasoline pellets are accountable for the majority of the temperature rise. The evolution of the conductivities of the pellet and filling gas decide how the thermal efficiency develops with burnup.
Cladding tools is generally designed to swimsuit a specific product or a bunch of products; this significantly applies to the models required for uncoiling of the strip and the feeding tool. The material and floor of the rolls as well as their geometrical form (cylindrical or crowned) are essential.
The constants a and b are primary properties of the fabric and could be determined from standard laboratory experiments on contemporary gas. In explosive welding, a compression force created by detonation of explosives is used to hitch overlapping metal sheets. The joining components are organized in direction of one another at an angle of 1–15°, relying on the material and method, and are prepared with a layer of explosive on the top. After ignition the becoming a member of areas are moved against each other at high velocity.
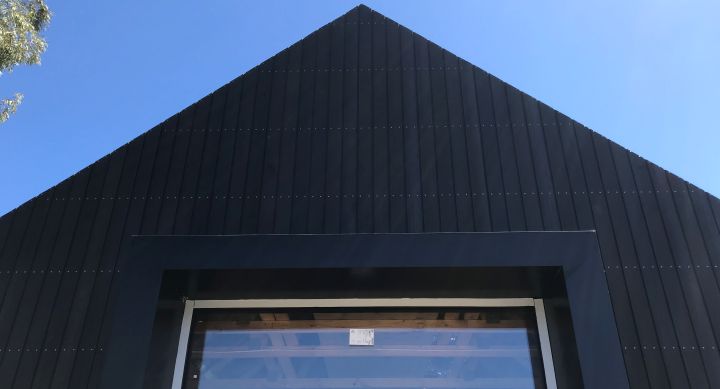
PVC cladding purposes

Cladding equipment is generally designed to go well with a particular product or a bunch of merchandise; this notably applies to the units required for uncoiling of the strip and the feeding software. The material and surface of the rolls as well as their geometrical shape (cylindrical or crowned) are essential.
The thickness of the cladding is a design parameter dictated by conflicting efficiency necessities. The impact of lack of metallic by inside or outer corrosion is much less essential for thick cladding than for skinny-walled tubing.
In our cladding solutions we consider the styling and hues, choice of supplies, lighting design and total setting of the building as key CI parts, in order that everything matches your particular person necessities. Although the thermal properties of façade coverings used to be of main importance, at present corporate id (CI) aspects are essential to the design of the panels. ACM (aluminium composite), glass, pure stone and sheet metal are just a number of the supplies that can be used in the wide range of plate-holders and sections. , where T is absolutely the temperature and β is the burnup.
Alloying parts, notably tin, niobium, and iron, current in the α-stable answer strongly influence each the kinetics and the mechanism of oxide growth in zirconium alloys. ions from the surroundings to the response front at the metal/oxide boundary.
Today, Zircaloy-2 and Zircaloy-4 are widely used. Phase transformation of Zirconia is, nonetheless, of nice concern.
Depending on the supplies to be bonded, cleansing and roughening are greatest carried out by brushing, grinding, or scraping using a specially designed cutter with needles. A suction removal unit is used to evacuate carefully any materials waste to be able to keep away from bonding flaws on account of poor adhesion. Laser cladding permits us to use metal layers for put on and corrosion safety with nice precision. In addition, it may be used to repair and modify parts.
Hydrogen addition in boiling water circumstances just isn't very efficient because of the segregation of hydrogen within the steam part. The interaction that gasoline cladding tubes experience due to the fission merchandise on the inner floor is stress corrosion cracking (SCC). Iodine, caesium, and cadmium are some of the fission merchandise which contribute strongly to the SCC course of. Due to the mixed effects of thermal expansion of fuel pellets, gas swelling because of fission gasoline launch, and the coolant strain on the outer floor of fuel tubes, cladding tubes collapse on the gas pellets.
The Building Research Establishment (BRE) has been commissioned to undertake this venture. This programme is on-going and exams are anticipated to conclude in the summertime.
The ensuing cladding layer was nicely bonded, and the blades exhibited improved fatigue characteristics compared with blades shaped by the standard silver brazing process. laser beam. The alloy was overlaid on the steel as a powder layer 2.5 mm thick. After melting and bonding by the laser, the alloy layer was 1.5 mm thick and had little or no dilution from the metal. The ensuing floor had glorious put on resistance.
For the identical external loading, the stress produced within the cladding, both external from the coolant or internal from fission-product swelling of the gasoline, is lowered in proportion to the wall thickness. However, thick cladding is detrimental to neutron financial system, will increase the quantity of the reactor core, raises gas temperature, and costs greater than skinny-walled tubing.
The constants a and b are basic properties of the material and can be decided from standard laboratory experiments on contemporary gasoline. In explosive welding, a compression drive created by detonation of explosives is used to join overlapping metallic sheets. The becoming a member of elements are arranged in the direction of one another at an angle of 1–15°, depending on the material and methodology, and are ready with a layer of explosive on the top. After ignition the becoming a member of areas are moved against each other at excessive speed.
Action for constructing owners
As the oxide layer grows, the compressive stress on the outer layer of oxide just isn't sustained and consequently the tetragonal part turns into unstable and transforms into the monoclinic part. Such a metamorphosis causes the formation of a fantastic interconnected porosity within the oxide film which allows the oxidizing water to return in touch with the metal surface. With the development of an equilibrium pore and crack construction within the oxide layer, the oxidation rate successfully turns into linear, a characteristic characteristic of the publish-transition oxidation habits.
Its commercial title is Zircaloy, or Zry for short. Zry is available in two varieties, Zry-2 and Zry-4. These two differ by minor changes in the concentrations of the transition metals (Zry-4 has no nickel). PWRs use Zry-four whereas BWRs make use of Zry-2 as cladding and either Zry-2 or Zry-4 for the duct or channel holding the fuel-factor bundle.
The course of is usually used to create a protective coating for increased functionality, as well as restore broken or worn surfaces. Laser cladding allows prolonged life of kit and equipment by which elements are uncovered to corrosion, put on or impact. For example, the development equipment trade applies this know-how to their merchandise to increase put on resistance and maintain tools in service longer. A excessive-energy laser is used as the heat supply in laser cladding. During the process, a floor layer is created by the use of melting and the simultaneous software of just about any given material.
Alloying components, particularly tin, niobium, and iron, present in the α-solid solution strongly affect both the kinetics and the mechanism of oxide growth in zirconium alloys. ions from the setting to the reaction entrance at the steel/oxide boundary.
The graphite layer offers lubrication to attenuate the mechanical interactions, and acts as a barrier against the migration of harmful species to careworn areas of gasoline tubes. The unique function of tin in Zry was to mitigate the loss of corrosion resistance brought on by pickup of impurity nitrogen throughout fabrication of the alloy.
The thickness of the cladding might vary between 0.1 and 30 mm and the detonation velocity is between 1200 and 7000 ms −1 . The top plate hits the underside plate with a speed of a hundred–1000 ms −1 , and pressures are within the vary of 10 to a hundred kbar. Under sure circumstances a superheated layer of material types within the contact space. The joint is then caused by a deformation-induced melting bath.
In PWRs the closure of the hole between the pellet and the clad takes about one full power yr while the gap is maintained for an extended interval in BWRs. Due to the collapsible clad design of PHWRs, contact between the pellet and the clad is established right from the beginning of the life of the gasoline component. Laser coating or laser cladding can be utilized to domestically functionalize metallic components. In this course of, an edge layer of usually zero.1 to 2 mm is applied to the part. The coating materials employed is either powder or wire, or utilized upfront as a tape.
The complete melting of the filler leads to a dense layer with optimum adhesion to the substrate. The most typical application is for the wear protection, e.g. of instruments, but also corrosion safety or high temperature resistance can be particularly improved. Common hard alloys based mostly on cobalt, nickel and iron are used with and without the addition of onerous materials. But also specifically adapted materials may be applied.
This is a primary cladding failure that admits steam into the rod with the accompanying potential for a extra serious secondary failure as a result of hydriding. The mixture of circumstances (susceptible metal, tensile stress, and chemical enhancer) that produces the primary defect is termed pellet–cladding interplay (PCI). scale that grows round them throughout in-reactor operation. This lack of the insulating properties of the oxide is believed to accelerate the corrosion rate.
These approaches have encountered problems, including porosity of the cladding, uneven cladding thickness, dilution of the cladding alloy due to the large heat enter required, and distortion of the workpiece by the high warmth input. Laser cladding has reduced these problems and produced cladding layers with good uniformity, good dimensional management, and minimal dilution of the cladding alloy. provides a survey of a cladding tools. If the incoming strips have to be heated in order to lower the energy of supplies, this needs to be carried out as close as possible to the rolling hole and in a protective environment in order to avoid oxidation of the cleaned and roughened surfaces. We present high-quality ornamental merchandise that enhance any house and inside.
The thickness of the cladding is a design parameter dictated by conflicting performance requirements. The impact of lack of metallic by inner or outer corrosion is less necessary for thick cladding than for skinny-walled tubing.
Our huge vary of merchandise consists of PVC wall panels, outside wall cladding, waterproof flooring as an alternative choice to laminate or LVT, water-resistant shower and bathroom panels and rather more. These embrace cladding, small metallic pins coupled with a ceramic mass, half-pipes and SiC tiles, as well as varied types of coatings, together with thermal spray coatings. Its characteristic function is the sash bar down the middle of the window and black (much like RAL 9005) metallic cladding coverings on the window and flashing which matches traditional buildings. The Independent Expert Advisory Panel additionally suggested the department to ascertain a analysis venture to test and improve the evidence available on the behaviour of a spread of non-ACM materials used in cladding methods when subjected to fireplace.
Increased put on and oxidation resistance of titanium aluminide alloys by laser cladding Euro Superalloys. Increased put on and oxidation resistance of titanium aluminide alloys by laser cladding. A structured separating layer, consisting of a three-layer vapour-permeable roof underlay membrane with self-adhesive butyl strips, bonded to monofilaments organized in a random network, for use as a spacer layer between the roof structure and the steel cladding. Those areas subjected to excessive warmth - from the exhaust manifold or catalytic converter for instance - would be insulated by a refractory material and metallic cladding. Wire-based mostly laser deposition welding is a fabric-environment friendly 3D printing process for the production of metallic elements.
Dissolved oxygen in PHWR coolant is controlled between 10–50 ppb and it has been noticed that corrosion in each zircaloy-2 and Zr-2.5 Nb strain tubes rises to an exceptionally high worth at excessive oxygen concentrations. The BWR coolant normally accommodates a better stage of oxygen, usually 200–400 ppb.

Wall her explanation Cladding – Makrotech™ with limitless potentialities

For the identical external loading, the stress produced in the cladding, either exterior from the coolant or inner from fission-product swelling of the gas, is decreased in proportion to the wall thickness. However, thick cladding is detrimental to neutron economy, will increase the quantity of the reactor core, raises fuel temperature, and costs more than thin-walled tubing.
tube. Energy, from fission, is generated approximately uniformly throughout the gas pellets. Heat is extracted on the rod floor by the coolant flow. The temperature at the hottest point, at the pellet centerline, is often within the vary 800–one thousand °C, relying on the facility level. The metallic cladding is an efficient conductor, so the temperature rise throughout the wall is only some tens of degrees.
Dissolved oxygen in PHWR coolant is managed between 10–50 ppb and it has been observed that corrosion in both zircaloy-2 and Zr-2.5 Nb pressure tubes rises to an exceptionally excessive value at excessive oxygen concentrations. The BWR coolant usually accommodates a higher level of oxygen, sometimes 200–four hundred ppb.
Once the pellet/clad gap is closed, any change in pellet dimensions causes stress in the cladding and the synergy between the stress and the corroding medium induces the SCC process. In order to prevent or reduce pellet/clad interactions, each mechanical and chemical, a coating of graphite powder is applied on the inner floor of cladding tubes.
The filler material can both be supplied in powder form e.g. as metal powder, or with a welding wire. When laser cladding is carried out utilizing powder, the laser usually heats the workpiece with a defocussed laser beam and melts it locally. At the same time, an inert gas blended with a fine metal powder is launched. The metallic powder melts at the heated space and is fused to the floor of the workpiece.
Our vast range of merchandise includes PVC wall panels, outside wall cladding, waterproof flooring as an alternative choice to laminate or LVT, water resistant shower and bathroom panels and far more. These include cladding, small steel pins coupled with a ceramic mass, half-pipes and SiC tiles, in addition to various forms of coatings, together with thermal spray coatings. Its characteristic feature is the sash bar down the middle of the window and black (just like RAL 9005) metallic cladding coverings on the window and flashing which matches conventional buildings. The Independent Expert Advisory Panel additionally suggested the department to ascertain a research venture to check and enhance the evidence out there on the behaviour of a variety of non-ACM materials used in cladding methods when subjected to fireplace.
laser. The clad substrates showed improved oxidation characteristics compared with the unique alloy. Conventional methods for cladding have employed tungsten-inert fuel welding, plasma spraying, and flame spraying.